A large European manufacturing group set out to improve operational efficiency across its international production network. Facing variability in performance across sites, the company partnered with PDM to roll out a hands-on LEAN-based OEE (Overall Equipment Effectiveness) improvement program. The initiative resulted in measurable gains in productivity, throughput, and engagement. All within one year.
The client is a leading European manufacturer of heating and comfort solutions with multiple production facilities across the continent. Operating in a competitive, cost-sensitive market, this manufacturer relies on high operational efficiency and timely deliveries. Each factory has its own legacy processes and performance challenges, creating the need for a harmonized approach to improvement across locations.
challenges
Four of the client’s production plants in Europe had inconsistent OEE levels, frequent changeovers, and missed productivity targets. Manual practices, limited visibility, and inconsistent stakeholder involvement hindered sustainable performance. The challenge was to develop a program that delivered local results while building a consistent LEAN foundation across all sites.
PDM'S APPROACH
PDM was brought in as a hands-on partner to provide LEAN expertise, enable internal ownership and sustainable change. Rather than applying a top-down model, PDM worked side-by-side with teams on the shop floor, guiding them through the tools, data, and behaviors that make continuous improvement stick. The program included:
- Pilot learning: PDM started with a successful pilot at one production line in Belgium. The experience, learnings, and tools from that pilot were refined and scaled for implementation at three additional sites across Europe.
- Implementation: Each site received a tailored plan focused on improving OEE, reducing changeover time (through SMED methodology), and increasing line productivity. Two changeover reduction projects were executed per production line, leading to faster transitions and less downtime.
- Engagement: Daily LEAN room meetings involving all key disciplines were introduced to shift performance management from reactive to proactive. Operators were engaged in defining issues and co-creating solutions, supported by workshops, coaching, and change management.
- Central monitoring, local ownership: An OEE monitoring framework and improvement routines were introduced for all plants. Local teams owned their KPIs, while PDM facilitated cross-site knowledge transfer and governance.
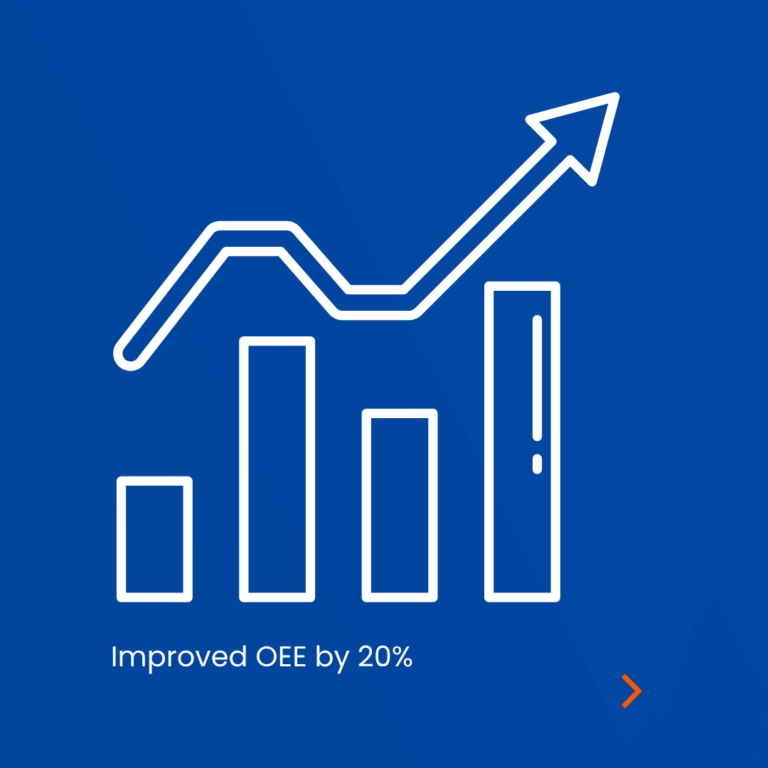
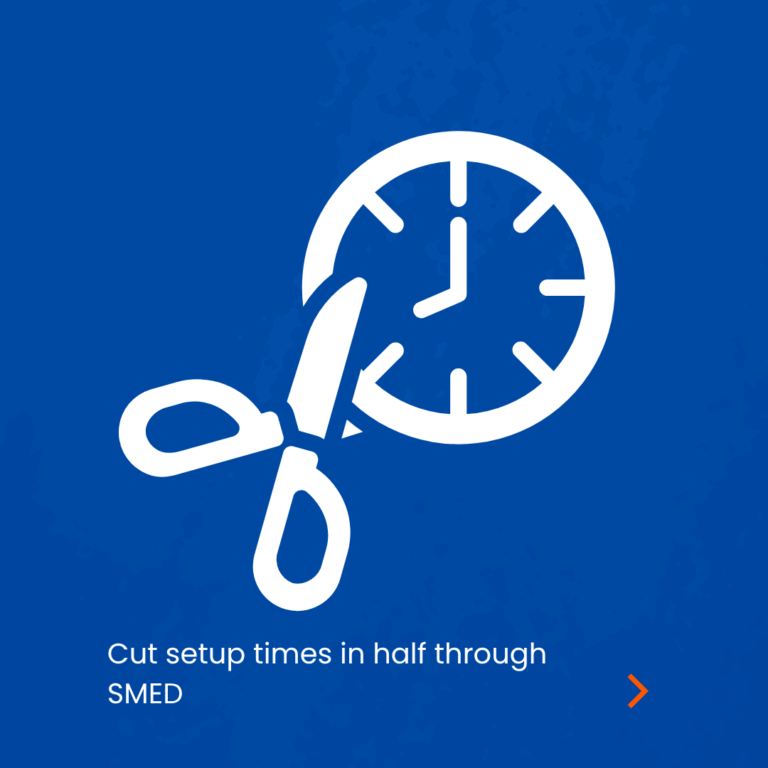
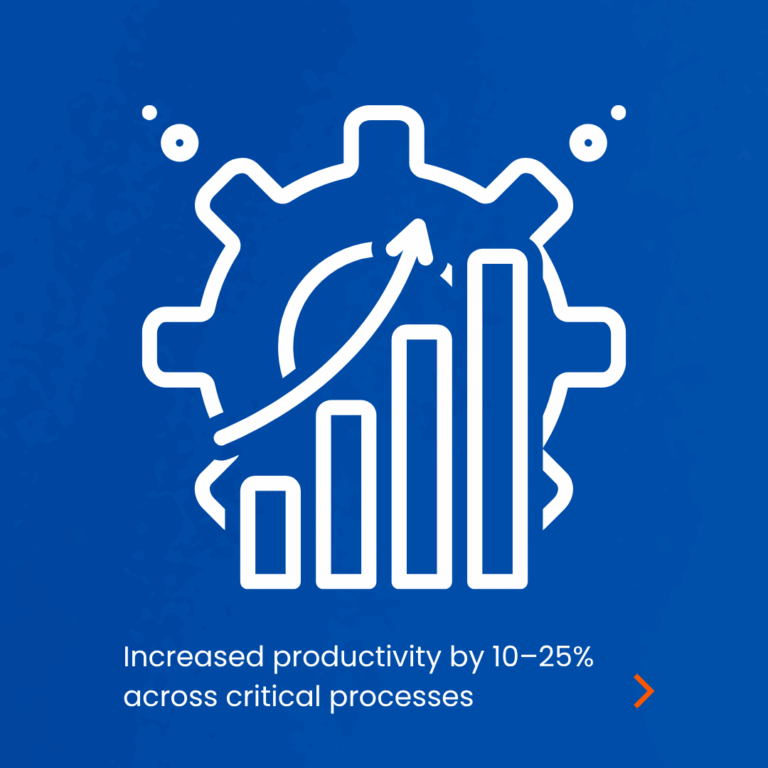
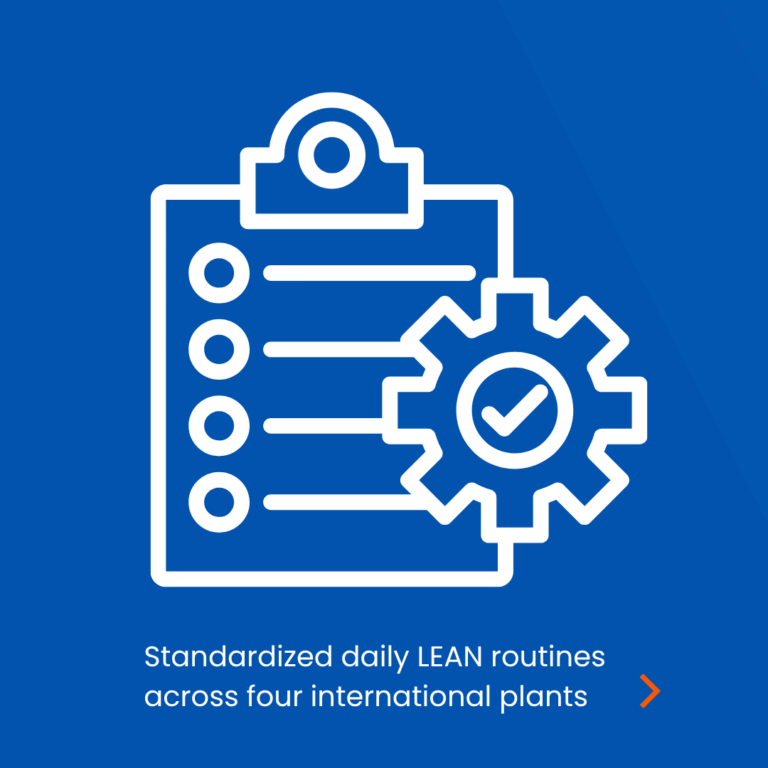
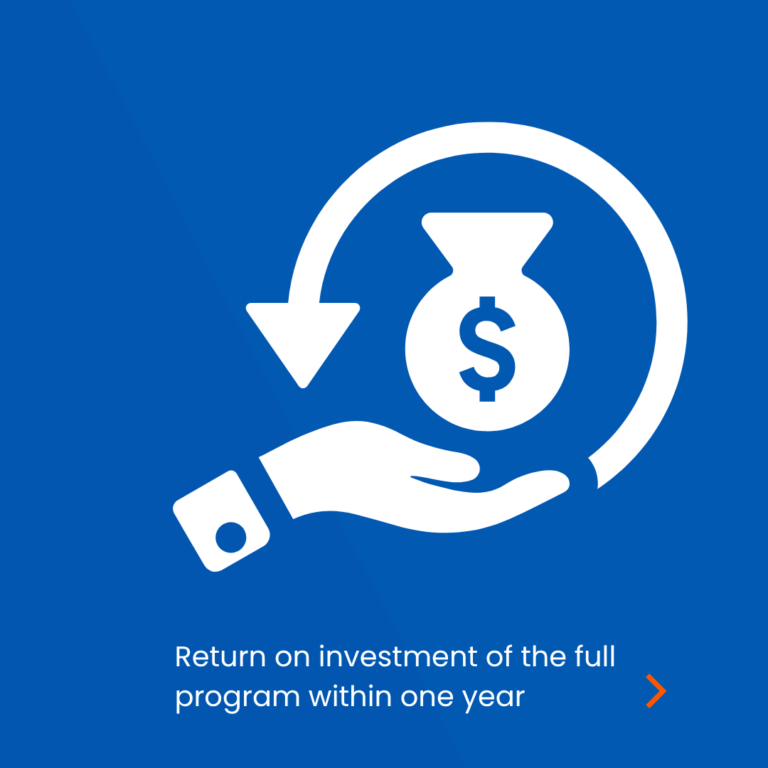
results & impact
The program produced strong quantitative and qualitative outcomes:
- OEE improved by 15–20% across pilot and follow-up lines
- Flat tube line productivity increased by over 10%
- Productivity at certain processes improved by more than 25%
- SMED projects halved setup time in multiple lines
- All four plants implemented daily LEAN meetings as standard operating rhythm
- Full cost recovery of the program within 12 months
The structured yet flexible approach allowed each site to benefit from centralized tools while applying them to local conditions. At one plant a line was shut down due to improved capacity on others, resulting in direct labor savings. In another plant, small-group activities led to a 10% rise in productivity. And at the third plant, despite already low labor costs, OEE and shop-floor engagement led to productivity gains over 25% and improved morale.
“The program brought structure in our improvement routines and introduced a clear and visual way of working with OEE, resulting in higher engagement and measurable improvement on the production lines.”
Operations Director
This case shows how LEAN programs can expose hard truths: fragmented routines, resistance to change, and underused shopfloor knowledge. PDM tackled these issues by building trust, clarifying KPIs, and facilitating structured problem-solving sessions across all plants. This highlights that the success of LEAN isn’t just in tools. It’s in ownership, persistence, and culture change.
conclusion
PDM’s structured rollout helped this international manufacturer measurably improve performance across four sites within one year, while building internal capability and cross-site alignment. The initiative didn’t just reduce waste; it built a culture of continuous improvement.
The program laid the foundation for future LEAN projects and internal LEAN agent training. Based on its success, similar approaches are now being considered at additional sites across the group. The initiative set the groundwork for forthcoming LEAN endeavors and the training of in-house LEAN agents. Given its accomplishments, comparable strategies are currently under review for implementation at other locations within the organization.
Curious how we could create results like this in your production environment?
Contact PDM to explore how our LEAN programs can boost your OEE, streamline changeovers, and empower your teams.
Or ready to take the lead on programs like this yourself?
As as Sr Project Leader at PDM, you’ll lead complex, multidisciplinary projects in design and manufacturing. You’ll work closely with clients, build strong teams, and deliver measurable results that drive real change on the shop floor. Interested? Let’s talk.