Turnarounds
Turnarounds are major events, often due to their size, length of preparation, the costs, investments and loss of production involved, and mandatory inspections. And are also called ‘revisies’ (energy), ‘Stilstände’ (Germany) or shutdowns (chemicals). Turnarounds aim at long-term maintenance, improvements and upgrades. They’re a balancing act between production demand, high quality asset management, safe/SHE and reliable performance.
Challenges to be met and to navigate through are considerable:
- The risk of the domino effect during the execution and the limitations of learning curves due to the duration of intervals;
- The dynamics of lengthy preparations versus fast track execution; extending or reducing intervals; managing the chain of interdependent plants;
- Scope definition and freeze; planning, scheduling and cost management; availability of resources and contractors; contractor management; downtime versus availability;
- Balancing the focus between the turnaround itself and the long term objectives, SHEQ, reliability, asset management, and including the impact on the plant performance.
The management of a turnaround requires a specific form of project management, while at the same time requiring to being part of long term program management: strategic considerations, plant performance-, SHEQ-, asset management development.
The STOPflow model was developed by PDM, evolved as a proven and widely used methodology for preparing and managing major and minor turnarounds, and has become an industry standard. During the years PDM participated in and managed around 250 turnarounds on behalf of production companies.
Today our ability in turnarounds focuses on the challenges to be met, the navigations to be managed, empowering, improving and innovating the project management and last but not least connect to the long term strategic considerations and development.
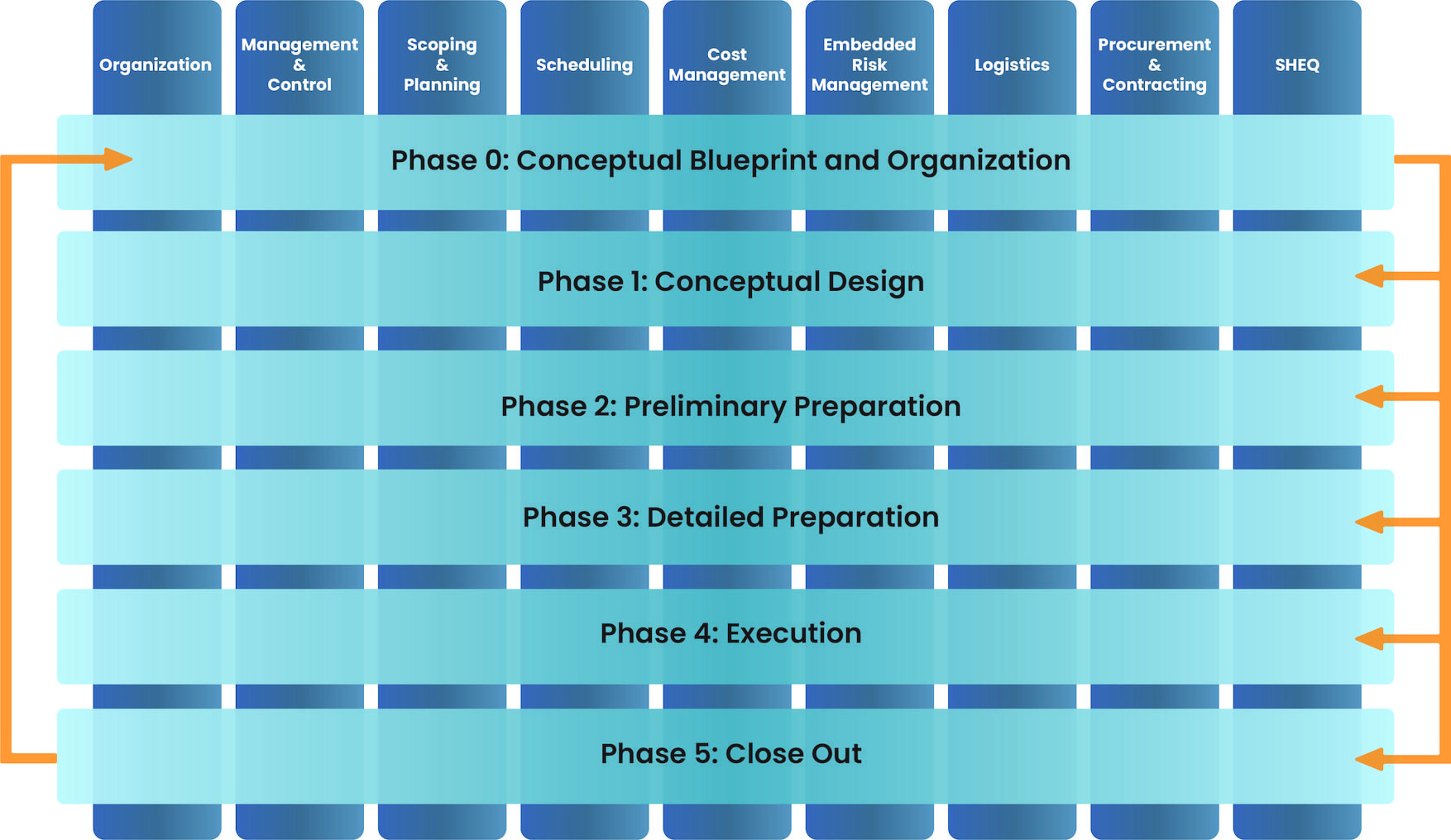